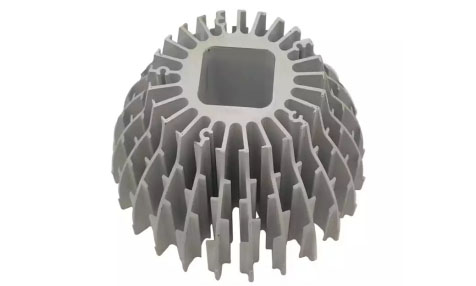
LED ഹീറ്റ് സിങ്കിന്റെ പ്രാധാന്യം
LED ഹീറ്റ് സിങ്ക്താപ വിസർജ്ജനത്തിനായി ഉപയോഗിക്കുന്ന ഒരു മെറ്റൽ പ്ലേറ്റ് ആണ്, സാധാരണയായി എൽഇഡി വിളക്കിന്റെ അടിയിൽ സ്ഥാപിച്ചിരിക്കുന്നു.എൽഇഡി ഉൽപ്പാദിപ്പിക്കുന്ന താപം ഫലപ്രദമായി ചിതറിക്കാനും പുറന്തള്ളാനും, സുരക്ഷിതമായ പരിധിക്കുള്ളിൽ എൽഇഡിയുടെ താപനില നിലനിർത്താനും എൽഇഡി വിളക്കിന്റെ സാധാരണ പ്രവർത്തനവും സേവന ജീവിതവും ഉറപ്പാക്കാനും ഇതിന് കഴിയും.
LED വിളക്കുകളുടെ തെളിച്ചവും ആയുസ്സും പ്രധാനമായും LED താപനിലയുടെ നിയന്ത്രണത്തെ ആശ്രയിച്ചിരിക്കുന്നു.ഉയർന്ന ഊഷ്മാവ് എൽഇഡി ലൈറ്റുകളുടെ തെളിച്ചവും ആയുസ്സും കുറയ്ക്കുകയും അവയുടെ പരാജയത്തിലേക്ക് നയിക്കുകയും ചെയ്യും.അതിനാൽ, LED ലൈറ്റുകളുടെ പ്രകടനത്തിനും വിശ്വാസ്യതയ്ക്കും LED ഹീറ്റ് സിങ്ക് നിർണായകമാണ്
LED ഹീറ്റ് സിങ്കിന്റെ പ്രധാന നിർമ്മാണ പ്രക്രിയ
LED ഹീറ്റ് സിങ്കുകൾക്കായി സാധാരണയായി ഉപയോഗിക്കുന്ന നിരവധി നിർമ്മാണ പ്രക്രിയകൾ ഇതാ:
1. എക്സ്ട്രൂഡഡ് ഹീറ്റ് സിങ്ക്
എക്സ്ട്രൂഡഡ് ഹീറ്റ് സിങ്ക്ആവശ്യമുള്ള ക്രോസ് സെക്ഷന്റെ ഒരു സ്റ്റീൽ ഡൈയിലൂടെ ചൂടുള്ള അലുമിനിയം ബില്ലെറ്റുകൾ തള്ളിക്കൊണ്ട് നിർമ്മിക്കപ്പെടുന്നു, തുടർന്ന് അത് അഭ്യർത്ഥിച്ച നീളമുള്ള ഹീറ്റ് സിങ്കിലേക്ക് മുറിക്കുക അല്ലെങ്കിൽ കാണുക.ഈ എക്സ്ട്രൂഷൻ പ്രക്രിയ സങ്കീർണ്ണമായ ഫിൻ ഡിസൈനുകൾ സൃഷ്ടിക്കാൻ അനുവദിക്കുന്നു.
2. കോൾഡ് ഫോർജിംഗ് ഹീറ്റ് സിങ്ക്
കോൾഡ് ഫോർജിംഗ് ഹീറ്റ് സിങ്ക്കോൾഡ് ഫോർജിംഗ് പ്രക്രിയയിലൂടെയാണ് നിർമ്മിക്കുന്നത്, സാധാരണ ഊഷ്മാവിൽ ഒരു പഞ്ച് ഉപയോഗിച്ച് അലൂമിനിയമോ ചെമ്പ് അസംസ്കൃത വസ്തുക്കളോ മോൾഡിംഗ് ഡൈയിലേക്ക് നിർബന്ധിച്ച് പിൻ ഫിൻ അറേകൾ രൂപം കൊള്ളുന്നു, പിന്നുകൾ അടിസ്ഥാന പ്രദേശത്ത് നിന്ന് നീട്ടട്ടെ.
3. ഡൈ കാസ്റ്റിംഗ് ഹീറ്റ് സിങ്ക്
ഉയർന്ന മർദ്ദത്തിൽ ദ്രാവക ഉരുകിയ ലോഹം ഉയർന്ന കൃത്യതയുള്ള അച്ചിലേക്ക് കുത്തിവയ്ക്കുന്ന നിർമ്മാണ പ്രക്രിയയാണ് ഡൈ കാസ്റ്റിംഗ്.വിശദമായ ഉപരിതല ഘടനയുള്ള സങ്കീർണ്ണമായ ത്രിമാന ഘടനകൾ നിർമ്മിക്കാൻ ഇത് പലപ്പോഴും ഉപയോഗിക്കുന്നു
LED ഹീറ്റ് സിങ്കിന് ഏറ്റവും മികച്ച നിർമ്മാണ പ്രക്രിയ ഏതാണ്?
എൽഇഡി ഹീറ്റ് സിങ്ക് ഒരേ രൂപത്തിലാണെങ്കിൽ, ഡൈ-കാസ്റ്റിംഗ് മോൾഡുകളുടെ വില ഉയർന്നതാണ്, കോൾഡ് ഫോർജിംഗ് അച്ചുകൾ മിതമായതാണ്, എക്സ്ട്രൂഷൻ മോൾഡുകളുടെ വില താരതമ്യേന കുറവാണ്.
പ്രോസസ്സിംഗ് ചെലവുകളുടെ വീക്ഷണകോണിൽ നിന്ന്, എക്സ്ട്രൂഷൻ പ്രൊഫൈൽ മെഷീനിംഗിന്റെ വില ഉയർന്നതാണ്, ഡൈ-കാസ്റ്റിംഗിന്റെ വില മിതമായതാണ്, ഫോർജിംഗിന്റെയും അമർത്തലിന്റെയും വില താരതമ്യേന വിലകുറഞ്ഞതാണ്.
മെറ്റീരിയൽ ചെലവുകളുടെ വീക്ഷണകോണിൽ നിന്ന്, ADC12 ഡൈ-കാസ്റ്റിംഗിന് മെറ്റീരിയൽ ചെലവ് താരതമ്യേന കുറവാണ്, അതേസമയം A6063 എക്സ്ട്രൂഷൻ, ഫോർജിംഗ് മെറ്റീരിയലുകൾക്ക് കൂടുതൽ ചെലവേറിയതാണ്.
സൂര്യകാന്തിപ്പൂക്കളുടെ ആകൃതിയിലുള്ള LED ഹീറ്റ് സിങ്കുകൾ ഉദാഹരണമായി എടുക്കുക.
എക്സ്ട്രൂഷൻ പ്രക്രിയയാണെങ്കിൽ, മെറ്റീരിയൽ പലപ്പോഴും A6063 ഉപയോഗിക്കുന്നു, ഉൽപ്പന്നത്തിന്റെ താപ വിസർജ്ജന പ്രഭാവം താരതമ്യേന മികച്ചതാണ്, കൂടാതെ ആനോഡൈസിംഗ് പോലുള്ള പൂർത്തിയായ ഉൽപ്പന്നത്തിന്റെ ഉപരിതല ചികിത്സ താരതമ്യേന എളുപ്പമാണ്.പൂപ്പൽ ഉൽപാദന ചക്രം സാധാരണയായി 10-15 ദിവസമാണ്, പൂപ്പൽ വില കുറവാണ്.
പോസ്റ്റ് മെഷീനിംഗ് ചെലവ് കൂടുതലും ഔട്ട്പുട്ട് കുറവുമാണ് എന്നതാണ് പോരായ്മ.
LED റേഡിയറുകൾ നിർമ്മിക്കാൻ ഡൈ-കാസ്റ്റിംഗ് ഉപയോഗിച്ച്, ADC12 മെറ്റീരിയൽ പലപ്പോഴും മെറ്റീരിയലായി ഉപയോഗിക്കുന്നു.
ഗുണങ്ങൾ ഇവയാണ്: കുറഞ്ഞ പ്രോസസ്സിംഗ് ചെലവ്, ഉയർന്ന ഉൽപാദന ശേഷി, പൂപ്പൽ അനുവദിച്ചാൽ റേഡിയറുകളുടെ വിവിധ രൂപങ്ങൾ നിർമ്മിക്കാനുള്ള കഴിവ്.
അസൗകര്യങ്ങൾ: പൂപ്പൽ വില കൂടുതലാണ്, പൂപ്പൽ ഉൽപ്പാദന ചക്രം ദൈർഘ്യമേറിയതാണ്, സാധാരണയായി 20-35 ദിവസം എടുക്കും.
കോൾഡ് ഫോർജിംഗ് കൊണ്ട് നിർമ്മിച്ച എൽഇഡി ഹീറ്റ് സിങ്ക് സൈദ്ധാന്തികമായി ഏത് മെറ്റീരിയലിലും നിർമ്മിക്കാം.
ഗുണങ്ങൾ ഇവയാണ്: കുറഞ്ഞ സംസ്കരണ ചെലവും ഉയർന്ന ഉൽപാദന ശേഷിയും.പൂപ്പൽ ഉൽപാദന ചക്രം സാധാരണയായി 10-15 ദിവസമാണ്, പൂപ്പൽ വില കുറവാണ്.
ഫോർജിംഗ് പ്രക്രിയയുടെ പരിമിതികൾ കാരണം, സങ്കീർണ്ണമായ ആകൃതികളുള്ള ഉൽപ്പന്നങ്ങൾ നിർമ്മിക്കാൻ കഴിയില്ല എന്നതാണ് പോരായ്മ.
ചുരുക്കത്തിൽ, എൽഇഡി ഹീറ്റ് സിങ്കിന് സങ്കീർണ്ണമായ രൂപവും വലിയ അളവും ഉണ്ടെങ്കിൽ, ഡൈ-കാസ്റ്റിംഗ് പ്രക്രിയ ഉപയോഗിക്കാൻ ശുപാർശ ചെയ്യുന്നു, എൽഇഡി ഹീറ്റ് സിങ്കിന് ലളിതമായ രൂപവും വലിയ അളവും ഉണ്ടെങ്കിൽ, കോൾഡ് ഫോർജിംഗ് പ്രക്രിയ ഉപയോഗിക്കാൻ ശുപാർശ ചെയ്യുന്നു,
അല്ലെങ്കിൽ, ഞങ്ങൾ പലപ്പോഴും എക്സ്ട്രൂഡഡ് പ്രോസസ്സ് ഉപയോഗിക്കുന്നു.അതേ സമയം, ഞങ്ങൾ നിർദ്ദിഷ്ട സാഹചര്യം വിശകലനം ചെയ്യുകയും വിലയ്ക്കും ഉൽപ്പന്ന പ്രകടനത്തിനും ഏറ്റവും അനുയോജ്യമായ നിർമ്മാണ രീതി തിരഞ്ഞെടുക്കുകയും വേണം.
ഹീറ്റ് സിങ്കിന്റെ തരങ്ങൾ
വ്യത്യസ്ത താപ വിസർജ്ജന ആവശ്യകതകൾ നിറവേറ്റുന്നതിനായി, ഞങ്ങളുടെ ഫാക്ടറിക്ക് താഴെപ്പറയുന്നതുപോലെ നിരവധി വ്യത്യസ്ത പ്രക്രിയകളോടെ വ്യത്യസ്ത തരം ഹീറ്റ് സിങ്കുകൾ നിർമ്മിക്കാൻ കഴിയും:
പോസ്റ്റ് സമയം: ഏപ്രിൽ-21-2023